Routing Basics
A routing defines the step-by-step operations you perform to manufacture a product. Each routing can have any number of operations. For each operation you specify a department that determines the resources you may use for that operation.
A primary routing is the list of operations most frequently performed to build a product. You can define one primary routing and many alternate routings an item. When you define a new primary routing, you specify only the item (no alternate name) and you can assign a routing revision. For example, you can define a routing for an item that includes two operations-an assembly and a testing operation. You typically build your product with these operations, so you define this routing as the primary routing for the item.
The following table presents an example primary routing.
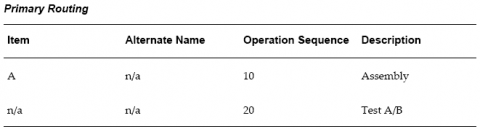
The following table presents an example of a primary and alternate routing for Item A.
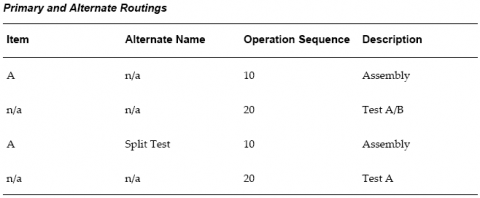
Creating a Routing
You can create a routing manually, copy an existing routing, or reference a common routing.
Prerequisites
1. You must define at least one department before you can create a routing.
2. BOM Allowed must be set to Yes for the item you are creating a routing for.
The procedure below describes how to manually create a routing.
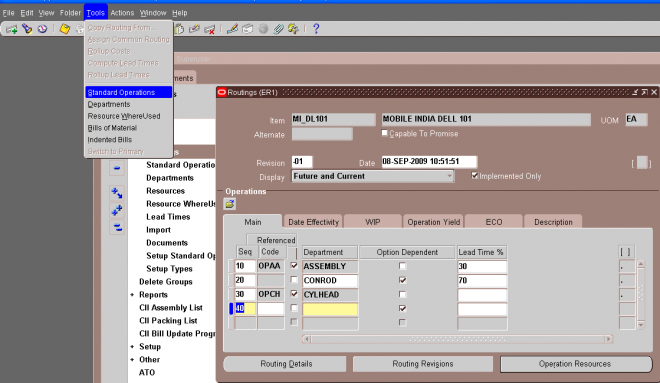
1. Enter a manufacturing item to create a routing for.
2. If you are creating an alternate routing, enter an alternate. For a primary routing, do not enter an alternate.
3. If you are updating an existing routing, enter the routing revision and the effective date.
To update the revision, choose the Routing Revisions button to open the Routing Revisions window.
4. If you would like this routing to be capable to promise, then select the Capable to Promise checkbox.
Note: Capable to promise describes an available to promise calculation that considers both available material and capacity of
manufacturing and distribution resources. You are able to define one and only one CTP routing for each item.
5. Select a display option to display All, Current, or Future and Current operations effective as of the revision date you specify.
Flexfield Value
Dear, i try to be able the flexfield value in the operation sequences, for example for operation 10 or 20 or other. Unfortunately i could not to get this action, i use table BOM_OPERATION_SEQUENCES. Could you please help me, how can i define this ? Thanks e Regards